豆知識・お役立ち情報
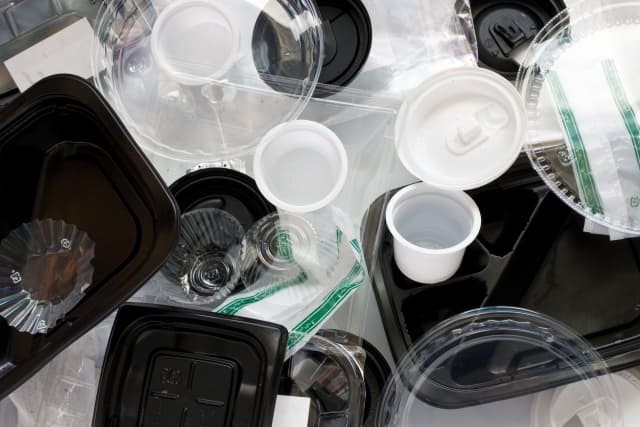
私たちの身の回りにある日用品や家電製品、雑貨など、多くの製品に使われているのが「射出成形」という加工法です。
今回は、射出成形の特徴や仕組みについてご説明いたします。
射出成形とは
射出成形(しゃしゅつせいけい)とは金型を使った加工法のひとつで、主に合成樹脂(プラスチック)の加工に使われています。
プラスチック部品を設計する際には、射出成形を利用するケースが多いことでしょう。
射出成形は複雑な形状のものでもスピーディーに大量生産することができるため、テレビや洗濯機、パソコンなどの電化製品やペットボトル、ハサミなど実に幅広い商品に用いられています。一度金型を作れば同じものを大量に作ることができるのが大きなメリットと言えるでしょう。
射出成形のメリット
複雑な形状にも対応可能
成形後の加工がほとんど必要ない
様々なサイズの成形品を作れる
素早く大量生産できる
一度金型を作れば、その後かかるコストは材料費のみ
加工の流れ
1.型締め
金型の締め付けが弱いと加工した時に出る残留物が製品に付着してしまいますので、金型をしっかりと締め付けます。
2.射出
ノズルを金型に押し付けて、溶かした合成樹脂を金型内に圧力で注入します。
3.保圧
射出したら金型に一定の圧力を加えて、合成樹脂が逆流しないようにします。
4.冷却
金型内の合成樹脂を冷却して、材料が固まるようにします。
5.型開き
冷却によって成形できたら金型を開きます。
6.製品の取り出し
成形品を取り出します。
射出成形の種類
射出成型が用いられる主な材料は、以下のように「熱可塑性樹脂」と「熱硬化性樹脂」の材質があります。
熱可塑性樹脂
ポリエチレン
塩化ビニル樹脂
フッ素樹脂
など
熱可塑性樹脂は温度が高くなると溶け、低くなると硬化します。そのため、射出成形では金型内で十分に冷却して成形してから取り出します。
冷却に一定の時間を要するため、少量生産や大型成形に向いています。
熱硬化性樹脂
エポキシ樹脂
ポリウレタン樹脂
シリコン樹脂
など
熱硬化性樹脂は温度が高くなると硬化し、硬化した後は液体に戻ることがありません。そのため、射出成形では熱硬化性樹脂が硬化する温度に設定した金型に熱硬化性樹脂を注入し、成形したら取り出します。
熱硬化性樹脂は熱可塑性樹脂のように冷却する必要がないため、大量生産に向いています。
射出成形機の構造
射出成形機は「型締ユニット」と「射出ユニット」に分かれています。
また、成形する際には射出成形機についているコントローラーを操作し、成形速度や圧力、温度、材料の射出量などの成形条件を指定します。
型締ユニット
型締ユニットは金型の装着や開閉、突き出しを行います。
また、成形後に成形品をピンで突き出して取り出しやすくするといった役割も果たします。
射出ユニット
射出ユニットは合成樹脂を加熱して溶かし、金型内へ注入する役割を担います。
材料の投入口となる「ホッパー」、材料を加熱する「シリンダー」、「噴射ノズル」などが含まれます。
まとめ
どのような形状・サイズでも素早く簡単に大量生産できる、といったように射出成形には様々なメリットがあります。
そのため、プラスチックの加工には様々な方法がありますが、そのなかでも射出成形は多くの加工で用いられているのです。
大量生産する場合にはコストも抑えられるため、製品の加工を考えている方は、ぜひ射出成形を検討してみてくださいね。